I have been contacted by several different Omni-E Faceting Machine owners. All of us have experienced water leaks and bearing problems on our machines, and those of us who have sent them back to the Jersey Instruments factory for repair have been told that we have flooded our bearings.
The owner of Jersey Instruments considers this owner abuse of the machine and charges for any repair work related to replacing the bearings.
As you will see from the following photos, I disagree completely. Due to a significant design flaw in the Omni Faceting Machine, I expect *EVERYONE* to have flooded bearings sooner or later. You are free to draw your own conclusions.
Please look carefully at this photo and tell me what your first thoughts are. I have cut 3 stones since getting it back from Jersey Instruments.
You are looking at the splash pan with the Spindle and Platen assembly removed.
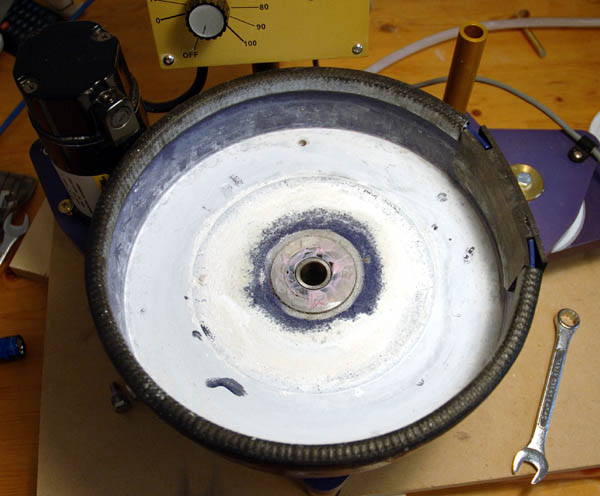
Here is a close-up of the Spindle Housing where it joins the Splash Pan. I have done nothing to it at this point except remove the Platen and Spindle.
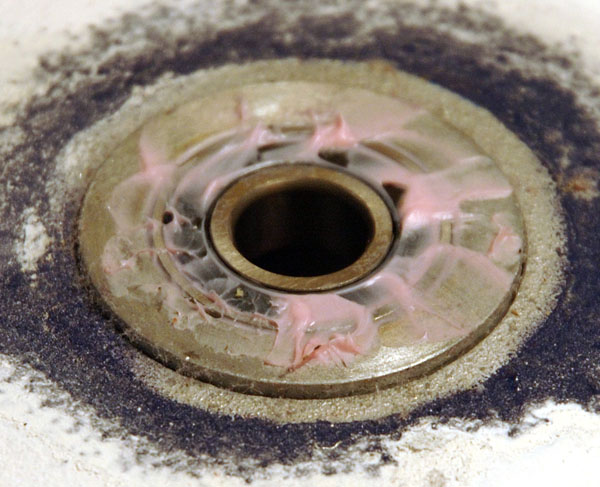
The pink smears are some sort of lithium grease. The webby-bits are lint and dust from the air, and the white stuff is ground gem dust.
Omni Bearing Design Flaw
There is no lip or any sort of rubber dam/gasket/barrier to prevent water from reaching the bearing or leaking down between the Spindle Housing and Splash Pan.
There is no protection to prevent water from reaching the Bearings.
The Splash Pan has a mild gradient to it, the center being about 1/8″ higher than the edge. But otherwise there is no protection for the Spindle Housing or bearings from water flooding. No rubber o-ring or gasket, not even a layer of grease to prevent water from flowing between the Splash Pan and the Spindle Housing.
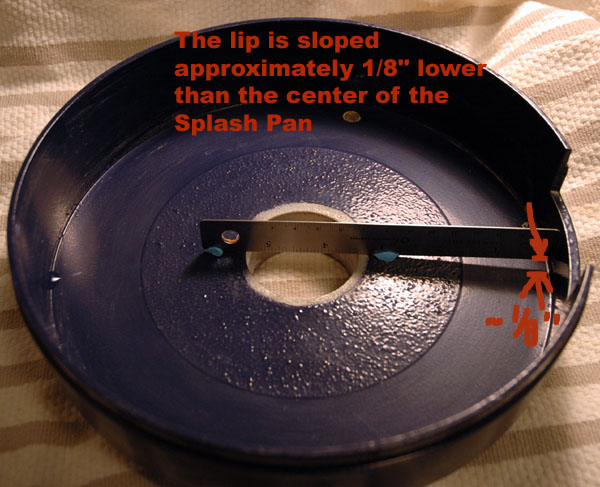
If you use a lot of water (when roughing for example) or your hose isn’t draining properly, you WILL flood your Spindle Housing and Bearings. There is nothing to prevent water from flowing there. Eventually, you WILL flood your Bearings and Spindle Housing. PERIOD.
Here is the Spindle Housing removed from the Splash Pan. As I stated above, I have cut 3 stones on the machine since it was returned to me from the factory.
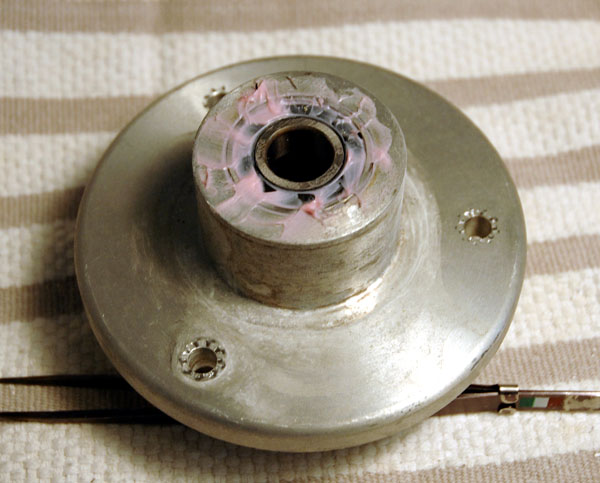
Note the rock powder and corrosion stains from water leaking between the Splash Pan and the Spindle Housing. This is a machined part – it should be completely smooth and shiny, not pitted and rough.
Here’s a side view close-up of the Spindle Housing. Notice how quickly the corrosion has started to pit the machined part.
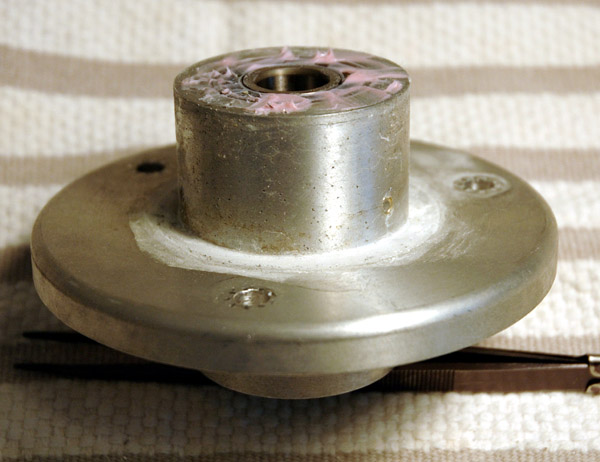
Here’s a close-up of the Splash Pan where it contacts the Spindle Housing. Notice the corrosion here too.
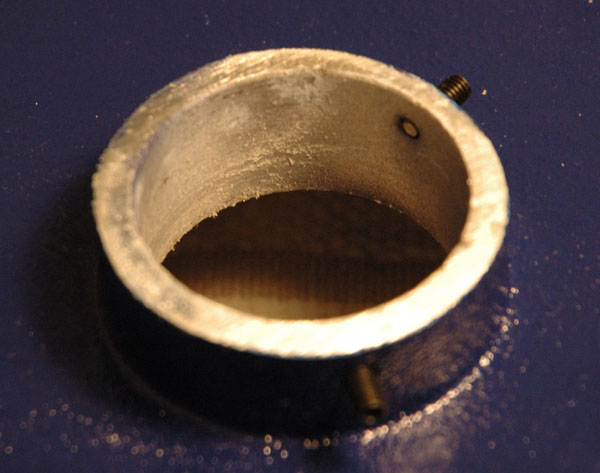
This is due to the two parts – the Spindle Housing and Splash Pan – being dissimilar metals. Add in a bit of water and you end up with galvanic corrosion occurring, causing the pitting.
Left long enough, this will destroy the Spindle Housing and Splash Pan. At very least, it will fuse the two together with corrosion. THIS SHOULD *NEVER* HAPPEN IN A GOOD DESIGN.
IS THIS THE SORT OF DESIGN YOU EXPECT FROM A PRECISION INSTRUMENT COSTING $2200?
There obviously was a reasonable amount of water that made it from my Splash Pan down the Spindle Housing to the Base, though not enough to drip into the bottom cover and wet my work table and alert me of the problem. You can see the beginning of rust and corrosion on the three set screws in this photo.
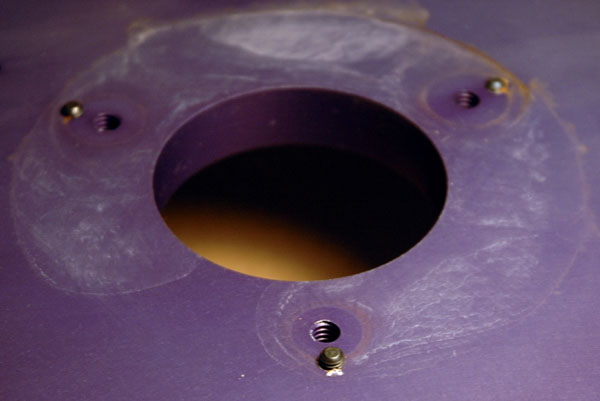
There should at least be a waterproof collar around the hole the Spindle Housing enters to prevent any water from making its way between the parts.
Suggested fixes (see the Omni Modifications section for details):
- Put a bit of silicon rubber sealer between the Splash Pan and the Spindle Housing to seal the gap (this won’t stop water from getting into the bearing if water gets this far)
- Put a bead of silicon rubber around the Splash Pan hole, say about 1″ from the edge. This will give the Platen enough clearance to not rub against it
- Create a new Splash Pan. I will be working on this in the coming weeks. I am thinking of a 4″ ID PVC tubing glued inside a 10″-11″ plastic container of some description.
Remember, I have only cut 3 stones so far. What would this look like after a year of cutting?
More important: Is this owner abuse of the machine? Or is it a “mechanical fault detrimental to the operation of the machine for which the manufacturer is responsible”?