I’ve had a few emails asking the best way to test the runout on your Omni faceting machine quill. I didn’t take any photos when I did it using a standard dial indicator and stand, and I don’t particularly recommend that method anyhow as it’s not very accurate.
If you have one of the new Omni faceting machines with the dial indicator for depth of cut, you’re in luck! Just put a dop in the quill and arrange the facet head and swing arm so the tip of the dop rests on the edge of a master lap. Leave the angle at 90 degrees and the facet head unlocked so the angle can change. Put the quill in free-wheel mode.
Rotate your dop on the master lap and watch the dial indicator. It will tell you how much wobble is in your quill, and what directions that wobble is worst.
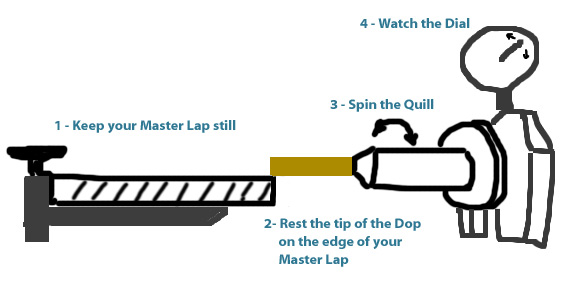
Using the Omni Faceting Machine Dial Indicator to Test Quill Runout
The best way to measure the quill runout is to use a lever dial indicator. Tom B. graciously allowed me to use his photo illustrating how he measured his quill runout on his faceting machine (not an Omni however). He clamped the lever dial indicator to the stationary portion of his faceting head then arranged the indicator so the tip of the lever rested on the barrel of the quill. Spinning the quill now will show you how much wobble is in your quill.
In the case of the Omni faceting machine, the best place to clamp the lever dial indicator is on the faceting head yoke – it’s the part that the quill fits into. Put the quill into free-wheel mode and measure away.
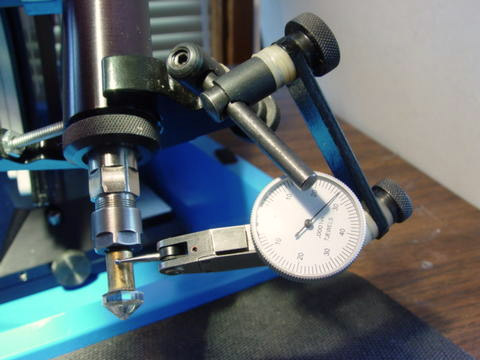
Measuring Quill Runout with a Lever Indicator
I hope your measurements are better than the others I’ve been hearing from. Collectively the average quill runout is 0.006″, which is a HUGE amount. I expect the quill runout to be under 0.001″ in order to cut to depth with any accuracy.
By the way – if you happen to own an Omni faceting machine with the depth-of-cut dial indicator AND you have a measurable quill runout, do you think your depth of cut indicator is going to do anything for you? You certainly aren’t going to be able to rely on it to tell you when you’ve reached the same depth of cut on each facet as that depth will change with every index position…